Industrial & Commercial Energy Use For Facility Energy Optimization
Energy usage in industrial and commercial sectors is becoming increasingly scrutinized. The US EIA stated in the International Energy Outlook Report that the industrial sector consumes about 54% of the world’s total delivered energy. And there are no plans to slow down. Energy consumption in the sector is expected to increase from 222 quadrillion BTUs in 2012 to 309 quadrillion BTUs in 2040. So how can we make the necessary changes for facility energy optimization?
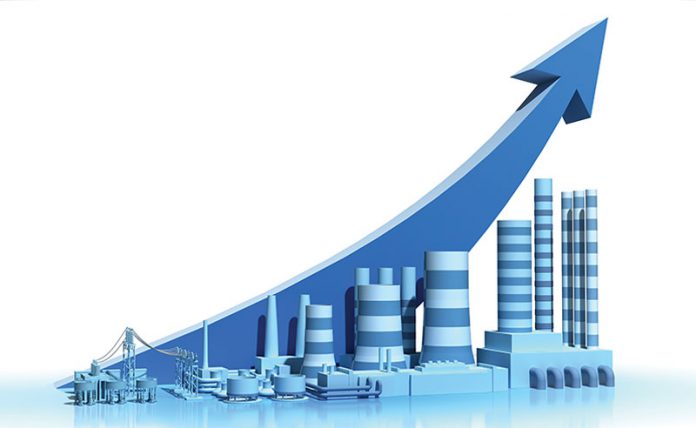
But with growing restraints on energy usage and the pressure to decarbonize, facilities must be designed and operated as efficiently as possible. Facility managers are struggling to find a balance between these opposing ideologies.
State of affairs
While traditional motivations behind energy efficiency and monitoring in plants are still fundamental, importance is now being placed on factors other than cost savings.
Effective energy management can reap the rewards from a reduction in energy waste to improved plant health to power factor optimization. But where to begin?
Setting baseline consumption levels is a good place to start when developing energy usage strategies. Then comes constant monitoring and regular reporting on results. Effective tracking of energy usage and comparing it against facility output goals help uncover issues in the system, reduce loss and mitigate risk.
It must be said that implementing such improvement strategies varies on a case-by-case basis. Facilities vary widely in age, type and complexity. As old plants reach maturity, pressure is being placed on facility operators to increase efficiency in systems which were not built with modern energy efficiency in mind. These complex plants and buildings may encounter various issues as they develop: ageing power cables, water damage, and faulty components. Who knows, rats could be chewing on a wire.
New facilities are being built with efficiency and sustainability targets in advance, with comprehensive monitoring, including SCADA systems that rival that of utility companies themselves. This wealth of information can be used to develop effective predictive and prescriptive models. On top of this, nowadays, building and plant designers are factoring rooftop solar, micro-grids and other modern technologies into architectural plans. With this intermittent generation source, more granular monitoring and maintaining balance are essential.
Importance of data

Data is the key. Understanding and leveraging the value of energy-flow data within the network can reap huge savings and rewards, even in the short term.
However, as facilities become modernized and, perhaps more importantly – digitized, it’s important that the digital representation of the network is correct. This begins with validating and correcting connectivity and topology accuracy across the network model. Many industrial plants have Single Line Diagrams, and it is valuable to have these updated, maintained, and verified. Having devices, motors, production lines, sensors and other network elements connected within the system, clear visualization and data transparency can be achieved – these assets become your digital twin inside your topology models.
New technologies
Automation, IoT and smart sensors have become everyday language in C&I facilities. These devices can be installed in new and old plants, and the data they provide unleashes a whole new realm of analytical capabilities.
What’s important is that tools which are used to monitor the system must be capable of ingesting and aggregating data from every device and technology which collects data. All data is useful. If any is left out, the resulting analytics may be inaccurate and counter-productive.
Contrary to the former point, however, it is better to get started analyzing the data that you do have, working towards quick simple wins. Building an iterative process, rather than trying to create a perfect solution, will help drive progress and keep you and your teams motivated throughout the process.
Once an automated data flow into such a tool is set up, energy flow can be visualized and understood from a different perspective. Energy consumption can be broken down by type of device, by section of the grid and by energy usage. By visualizing energy flow spatially, facility operators and energy managers can make more intelligent, data-driven decisions. This type of situational awareness is essential when responding to issues and diagnosing at-risk assets.
How to begin
Awesense’s True Grid Intelligence® (TGI) platform helps our Commercial and Industrial partners monitor their energy usage, detect issues in their network and improve energy efficiency across the board, helping facility energy optimization.
We work closely with operators and engineers to solve issues in both old and modern facilities. If an extra layer of visibility is required, Awesense Raptor Sensors can help.
With so much information flowing through the system, facilities need a solution to help make sense of that data. TGI does exactly that.
Our experts, software and hardware help to:
- Improve energy efficiency across the board
- Lower energy usage costs
- Diagnose and solve issues quickly and effectively
- Avoid power factor penalties
- Improve asset health and lifespan
- Reduce risk
If you need to monitor, analyze and optimize your facility’s energy usage, get in touch at sales@awesense.com.com